Comment bloc de béton est fait - la matière, la fabrication, utilisés, les composants, la structure, les étapes, la machine
Contexte
mortier de béton a été utilisé par les Romains dès 200 av. J.-C. pour lier des pierres en forme ainsi que dans la construction de bâtiments. Sous le règne de l'empereur romain Caligula, en 37-41 après Jésus-Christ. petits blocs de béton préfabriqué ont été utilisés en tant que matériau de construction dans la région de Naples, Italie actuelle. Une grande partie de la technologie du béton développée par les Romains a été perdu après la chute de l'Empire romain au Ve siècle. Il a fallu attendre 1824 que le tailleur de pierre anglais Joseph Aspdin développé ciment portland, qui est devenu l'un des éléments clés du béton moderne.
Le premier bloc de béton creux a été conçu en 1890 par Harmon S. Palmer aux États-Unis. Après 10 ans d'expérimentation, Palmer fait breveter en 1900. Palmer # x0027; les blocs de étaient 8 po (20,3 cm) de 10 po (25,4 cm) par 30 (76,2 cm), et ils étaient si lourds qu'ils devaient être levé en place avec une petite grue. En 1905, environ 1500 entreprises fabriquaient des blocs de béton aux États-Unis.
Ces blocs étaient généralement jetés début à la main, et la production moyenne était d'environ 10 blocs par personne et par heure. Aujourd'hui, la fabrication de blocs de béton est un processus hautement automatisé qui peut produire jusqu'à 2000 blocs par heure.
Matières premières
Le béton couramment utilisé pour fabriquer des blocs de béton est un mélange de ciment Portland en poudre, l'eau, le sable et le gravier. On obtient ainsi un bloc gris clair avec une texture de surface fine et une résistance à la compression élevée. Un bloc de béton typique pèse 38-43 lb (17,2 à 19,5 kg). En général, le mélange de béton utilisé pour des blocs a un pourcentage plus élevé de sable et un pourcentage plus faible de gravier et d'eau que les mélanges de béton utilisés à des fins de construction générale. Ceci produit un mélange très sec, rigide qui conserve sa forme lorsqu'il est retiré du moule de bloc.
Si le charbon granulé ou de cendres volcaniques sont utilisés à la place de sable et de gravier, le bloc obtenu est communément appelé un bloc de béton de mâchefer. Cela produit un bloc gris foncé avec une texture de surface moyenne à grossière, une bonne résistance, de bonnes propriétés insonorisantes, et une valeur d'isolation thermique supérieure à un bloc de béton. Un parpaing typique pèse 26-33 lb (11.8-15.0 kg).
Les formes et tailles de blocs de béton les plus courants ont été normalisés pour assurer la construction de bâtiments uniforme. La taille du bloc le plus courant aux États-Unis est appelé comme 8 par 8 par 16 bloc, avec les mesures nominales de 8 po (20,3 cm) de hauteur par 8 po (20,3 cm) de profondeur par 16 (40,6 cm) de large. Cette mesure nominale comprend la place pour un cordon de mortier, et le bloc lui-même mesure en fait 7,63 en (19,4 cm) de haut par 7,63 en (19,4 cm) de profondeur dans 15,63 (38,8 cm) de large.
De nombreux fabricants de blocs progressifs offrent des variations sur le bloc de base pour obtenir des effets visuels uniques ou de fournir des caractéristiques structurelles souhaitables pour des applications spécialisées. Par exemple, un fabricant propose un bloc spécialement conçu pour résister aux fuites d'eau à travers les murs extérieurs. Le bloc comprend un mélange hydrophobe pour réduire le béton # x0027; absorption s et une perméabilité, un bord supérieur biseauté pour évacuer l'eau loin du joint de mortier horizontal, et une série de rainures internes et des canaux pour diriger l'écoulement de toute fissure induite par fuite à une distance de la surface intérieure.
Une autre conception de bloc, un bloc appelé split-face, comprend une texture rugueuse, comme la pierre sur une face du bloc au lieu d'une face lisse. Cela donne au bloc l'aspect architectural d'une pierre taillée et habillée.
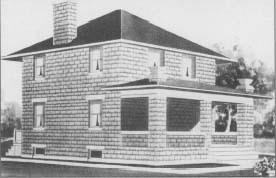
Une conception de maison de style Foursquare, apparaissant dans la Radford Architectural Company # x0027; de 1908 catalogue Maisons de ciment et comment les construire. Il était l'un des centaines de modèles de maison de bloc cancrete offerts par la société Radford. Ils ont estimé que cette conception pourrait être construit pour environ $ 2,250.00, beaucoup moins que les maisons traditionnelles de maçonnerie en pierre de l'époque.
(A partir des collections de Henry Ford Museum # X0026; Greenfield Village.)
Des blocs de béton ont d'abord été utilisés aux États-Unis en tant que substitut de la pierre ou du bois dans la construction de maisons. Le premier exemple connu d'une maison construite dans ce pays tout en blocs de béton était en 1837 sur l'île de Staten, New York. Les maisons construites de blocs de béton ont montré une utilisation créative des matériaux peu coûteux communs fait pour ressembler à la construction de maçonnerie en pierre à ossature de bois plus cher et traditionnel. Ce nouveau type de construction est devenu une forme populaire de la construction de maisons au début des années 1900 dans les années 1920. styles maison, souvent appelés « moderne » à l'époque, allaient de Tudor à Foursquare, néo-colonial à Bungalow. Bien que de nombreuses maisons ont utilisé les blocs de béton en tant que structure, ainsi que la surface de paroi extérieure, d'autres maisons utilisées stuc ou d'autres revêtements sur la structure de bloc. Des centaines de milliers de ces maisons ont été construites en particulier dans les États du Midwest américain, probablement parce que les matières premières nécessaires à la fabrication des blocs de béton étaient en abondance dans les bancs de sable et de gravières dans cette région. Les blocs de béton ont été faites avec des dessins de visage pour simuler des textures de pierre: rock-face, face granit, ou rustiquée. Tout d'abord considéré comme un matériel expérimental, les maisons construites de blocs de béton ont été annoncés dans de nombreux fabricants de ciment portland # x0027 de; catalogues comme « l'épreuve du feu, la preuve de la vermine et aux intempéries » et comme un remplacement bon marché pour la fourniture de plus en plus rare du bois. De nombreux autres types de bâtiments tels que les garages, les silos et les bureaux de poste ont été construits et continuent d'être construits aujourd'hui en utilisant cette méthode de construction en raison de ces qualités.
Lorsque les fabricants conçoivent un nouveau bloc, ils doivent prendre en compte non seulement la forme désirée, mais aussi le processus de fabrication nécessaire pour faire cette forme. Les formes qui nécessitent
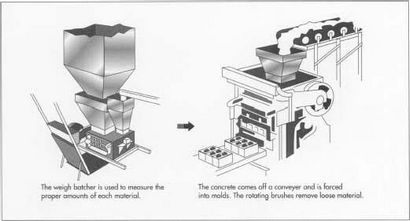
la fabrication
Processus
Les étapes suivantes sont couramment utilisées pour la fabrication de blocs de béton.
- 5 Une fois que la charge de béton est mélangé à fond, il est déversé dans un inclinée
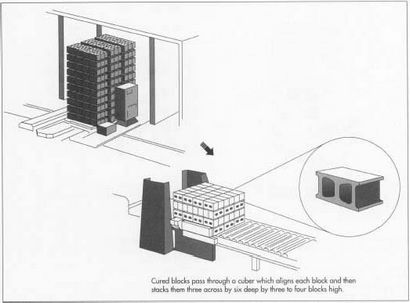
- 9 Les palettes de blocs sont transportés vers un empileur automatique ou chargeur qui les place dans une armoire de séchage. Chaque rack détient plusieurs centaines de blocs. Quand un rack est plein, il est enroulé sur un ensemble de rails et déplacé dans un four de durcissement.
10 Le four est une chambre fermée avec la capacité de contenir plusieurs supports de blocs à la fois. Il existe deux types de fours de séchage. Le type le plus commun est un four à vapeur basse pression. Dans ce type, les blocs sont maintenus dans le four pendant une à trois heures à température ambiante pour leur permettre de durcir un peu. La vapeur est ensuite introduit progressivement pour élever la température à une vitesse contrôlée de pas plus de 60 # XB0; F par heure (16 # XB0; C par heure). des blocs de poids standard sont généralement durcis à une température de 150-165 # XB0; F (66-74 # XB0; C), tandis que les blocs légers sont durcis à 170-185 # XB0; F (77-85 # XB0; C). Lorsque la température de durcissement est atteinte, la vapeur d'eau est coupée, et les blocs sont autorisés à tremper dans l'air chaud et humide pendant 12-18 heures. Après trempage, les blocs sont séchés par évacuation de l'air humide et d'élever davantage la température dans le four. Le cycle de durcissement dure environ 24 heures.
Un autre type de four est le four à vapeur à haute pression, parfois appelé un autoclave. Dans ce type, la température est élevée à 300-375 # XB0; F (149-191 # XB0; C), et la pression est portée à 80-185 psi (05.05 à 12.08 bar). Les blocs sont autorisés à tremper pendant cinq à 10 heures. La pression est alors évacué rapidement, ce qui provoque les blocs de libérer rapidement leur humidité piégées. Le processus de durcissement de l'autoclave nécessite plus d'énergie et un four plus cher, mais il peut produire des blocs en moins de temps.
- 11 Les supports de blocs durcis sont roulés sur le four, et les palettes de blocs sont dépilés et placé sur un convoyeur à chaîne. Les blocs sont poussés hors des palettes en acier, et les palettes vides sont introduits dans la machine de bloc pour recevoir un nouvel ensemble de blocs moulés.
- 12 Si les blocs doivent être faits en blocs split-face, ils sont d'abord moulées sous forme de deux blocs reliés entre eux. Une fois ces doubles blocs sont guéris, ils passent par un séparateur, ce qui les frappe avec une lame lourde le long de la section entre les deux moitiés. Cela provoque la double bloc à la rupture et former une texture rugueuse, comme la pierre sur une face de chaque pièce.
- 13 Les blocs passent par un cuber qui aligne chaque bloc et les empile dans un cube en trois blocs à travers six blocs profonds par trois ou quatre blocs de haut. Ces cubes sont portés à l'extérieur avec un chariot élévateur et placé dans le stockage.